Presses and Press Forming
1. How a Press Works
Contributing to Manufacturing Industries Worldwide
Many people may ask, “What exactly is press forming?” In press forming, a pair of tools called a “die” is mounted inside a press and then a material (such as metal) is placed inside the die. The press then applies high pressure (3000 tons of force or higher on large presses) and the material is formed to match the shape of the die. In other words, press forming is a forming technology where a pressing force is applied to a material to deform it (by bending, stretching, etc.) to match the size and shape of the die, and the material then maintains that shape forever.
Presses are suited for mass production because press forming can quickly produce the same product over and over again, and presses are widely used around the world in the automotive industry as well as in the factories of other industries.
The Press Forming Process
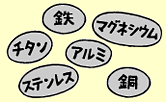
The materials are primarily metals.
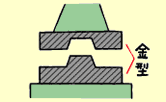
The upper and lower sections of a die are mounted inside the press
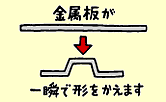
The die sandwiches the metal and pressure is applied
2. Press Products are All Around You
Presses are Used to Manufacture a Diverse Array of Products
A wide array of products of different sizes can be formed using presses, ranging from simple shapes requiring a single process to more sophisticated products requiring multiple processes. The flexibility provided by press forming in terms of product design and size enables the manufacture of a diverse range of products.
Japanese Vehicles are the Most Diverse in the World
The Japanese automotive industry manufactures the most diverse types of vehicles in the world. Recently, there has been a noticeable trend towards promoting differentiation by adding functions to meet the diverse needs of consumers in each of the world markets. And the efficient and flexible manufacturing structure of the just-in-time production system is also a hallmark of the Japanese automotive industry. AIDA's high-performance forming systems are instrumental in enabling the versatile and flexible manufacturing systems that are used in the automotive industry.
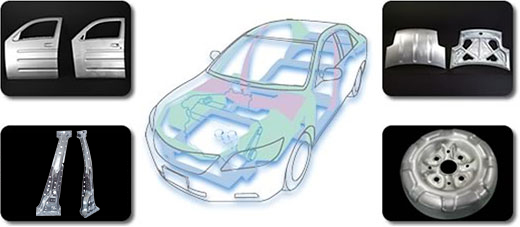
A Diverse Array of Home Appliances
Flat-screen TV body panels and built-in compressors for refrigerators, air-conditioners, and washing machines are manufactured by press forming. Utilizing the distinct advantages of press forming to achieve quick delivery and mass production, many products with diverse designs can be manufactured and placed on the market in rapid-fire succession.
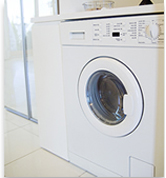
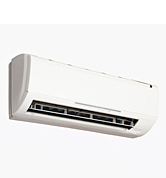
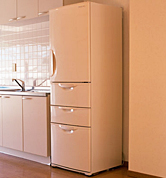
Electronic Components Such as IC Chip Frames and HDDs
The production of the lead frames used to mount integrated circuit (IC) chips require micron-level accuracy (one micron = 1/1000 mm) and ultra-precise die assembly and press forming technologies. Many other electronic equipment components are manufactured by press forming, including computer components, such as hard disk drives (HDD's), and lithium-ion battery cases for cell-phones.
Items in Your Kitchen and Your Wallet Too!
Products formed using presses turn up in the most unlikely places. For example, titanium eyeglass frames and wristwatch cases and stainless steel cooking pots, knives, spoons, and doorknobs. Even coins are made using presses.
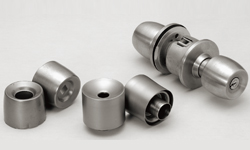
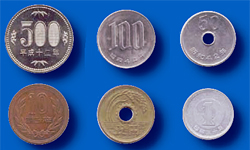
AIDA Technologies in Our Daily Life
3. High-Precision Presses
Advanced Technologies to Support Product Evolution
In recent years the automotive industry has been taking environmental concerns into consideration, and has been promoting automotive production that uses light yet strong materials to improve gas mileage and thereby reduce CO2 emissions, and since they are now using more lightweight high-strength materials that are more difficult to form, even more advanced press forming technologies have become necessary. Additionally, in recent years it has become possible to form even difficult-to-form materials that could not be formed using conventional presses, such as titanium alloys used for watch cases and the magnesium alloys used to make the lightweight cell phones and computers that consumers crave.
Another example is a motor core (electrode) used for the motor of a hybrid car. This requires a precise and delicate process technique to laminate multiple ultra-thin metal plates and only a press can be used to achieve this result.
These next-generation press forming technologies support the enhanced performance and multifunctional abilities of products such as these.
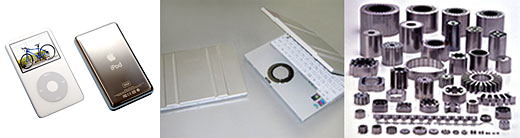
4. Our Business Directly Contributes to a Better Environment
Meeting the Resource and Energy Conservation Requirements of the Age
Today, the earth is beset with various environmental problems such as global warming. The manufacturing industries also bear some of the responsibility to resolving such issues, and they are required to contribute to environmental protection as part of their business activities regardless of their type of business. AIDA's press forming production methods conserve energy and resources, and this directly contributes to a better environment.
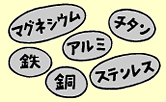
1.Uses recyclable metal materials
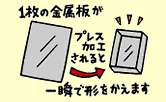
2.Very little trimming occurs during the forming process, resulting in minimal amounts of scrap.
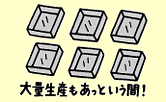
3.Rapid mass production with reduced energy consumption saves energy.