Forming Systems- Technology Development
Manufacturing Creative and Innovative Products Using Our Superior Technological Development Capabilities
As a specialized manufacturer of forming systems, AIDA has been actively involved in strengthening its R&D infrastructure with the aim of creating unique technologies and products in the metalforming field.
List of some of AIDA's “Japan firsts” and “First in the world” since its foundation in 1917
1933 | Manufactures the first Japan-built knuckle-joint press. |
---|---|
1951 | Manufactures the first Japan-built crown capping press. |
1955 | Manufactures the first Japan-built 200-ton high-speed automatic press. |
1960 | Manufactures the first Japan-built transfer press. Spearheads the spread of transfer press metalforming in Japan. |
1967 | Manufactures the world's largest-class (2,500-ton) transfer press. Achieves world-leading high-speed utilization performance in terms of productivity. |
1968 | Manufactures “Autohand,” Japan's first industrial robot, spurring the rapid expansion of the manufacturing robot industry. |
2000 | Independently develops a powerful low-speed, high-torque motor for servo presses. |
Entering the 21st century, AIDA has continued its cutting-edge R&D; direct-drive servo presses that leverage independently developed servo motors and control technologies, the “ultimate” UL X Series of presses that are more accurate than the die, and the Large Direct Servo Press, with a 2,300-ton capacity that places it in the world's largest class of servo presses..
We have won many awards for our products and our process technologies, and we have submitted approximately 500 patent applications in the last 10 years.
The AIDA Direct Servo Former with a Direct-Drive Servo Motor
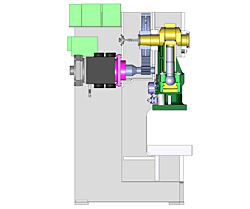
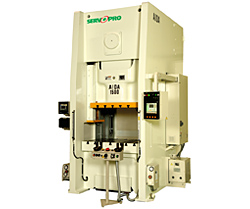
The AIDA UL* Series with a Unique 9-Point Support Mechanism
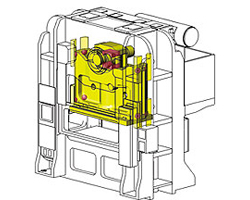
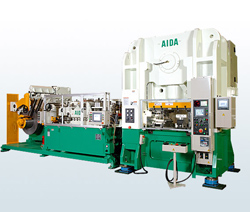
【Special Feature】 Servo Motors
AC Servo Motor Maximum External Dimensions: W 1.1 m x L 1.5 m x H 1.1 m.
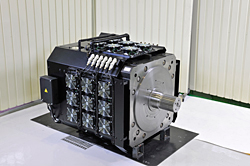
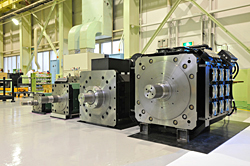
External View of High-Capacity Low-Speed, High-Torque AC Servo Motors
Development Background
When AIDA first began developing servo presses in the 1990s there were no servo motors in existence that were optimally suited for press metalforming applications. AIDA thus decided to independently develop its own servo motors, and this led to the development of AIDA's high-capacity, low speed, high torque (i.e., high output (see Note 1)) servo motors that could be used for direct-drive applications without requiring an intervening speed reducer.
Note 1: Using a bicycle as an example, torque is high when a strong force is being applied to the pedals.
At the time, the only servo motors on the market were high-speed motors equipped with speed reducers. In order to make a large servo press, AIDA determined that a motor that could generate high torque even at low speeds would be necessary, and moreover, in order to maintain high forming precision that a drive mechanism with the motor directly linked to it without an intervening speed reducer would be necessary. But unfortunately, there were no servo motors that could meet both of these requirements.
”We cannot compromise and use sub-optimal servo motors, as that would affect the basic performance of our servo presses. If these are not available on the market, we will make them ourselves.“ This spirited AIDA mindset towards manufacturing spurred its development of the world's most powerful classes of servo motors that are compact in size yet provide the necessary high capacity, low speed, and high torque characteristics. AIDA was also very particular about the conservation, generation and storage of energy-i.e., the motor features that would be advantageous to its customers.
Attention to such details truly epitomizes AIDA's approach to servo presses.
This was followed by the in-house development of not only motors but also peripheral equipment such as servo amps, power supplies, motor controllers and energy management systems that were then incorporated into a complete servo system package, and thus AIDA was able to offer a revolutionary system that could not only meet the usage requirements of presses but also the requirements for large industrial machinery as well as the requirements for equipment in many other industries.
Primary Features of AIDA AC Servo Motors
(1) The high capacity, low speed and high torque direct-drive mechanism assures higher productivity and formability.
Conventional servo motors have low torque even at high speed, and in order to use them on presses it requires a speed reducer to lower the speed (i.e., reduce the motor rpm and convert it to torque). However, having a speed reducer between the motor drive area and the area where forming is actually taking place could degrade the forming precision.
In order to achieve these contradictory requirements, AIDA decided to use a direct-drive system where the motor would be directly linked to the drive without using a speed reducer, and thereby enable the generation of strong drive power (high torque) at low speeds and also maintain high forming precision.(See Note 2)
Note 2: Think of this as the ‘Telephone (Grapevine) Game,’ where a message is relayed from person to person and the more people there are the worse the precision (accuracy) of the message becomes. If there were only one person relaying a message to only one other person, it would increase the precision of the message. This is the benefit of a direct-drive system.
(2) The motor's power regeneration feature enables the conservation, generation, and storage of energy.
In many cases, the motions of servo motor-equipped industrial machines only use energy momentarily when accelerating and decelerating and when forming. The energy management system of an AIDA servo motor effectively re-uses the electrical power that is regenerated (see Note 3) when the motor is decelerating, and the AIDA system also enables a large reduction in the required power supply equipment.
Note 3: Regenerated electrical power is excess electrical power that is generated by the machine and is returned to the system for reuse, and this regeneration feature increases the energy efficiency of the machine. This is the same thing that occurs in an electric car from the time the brake pedal is pushed until the car stops decelerating-i.e., energy is generated and returned to the car battery (the storage device) in order to maintain sufficient battery power.
Future Possibilities: A Major Evolution in the Application Possibilities--Transitioning from Servo Presses to All Types of Large Industrial Machinery
We are beginning to see a shift in the type of drive systems used for large machinery--a shift from hydraulic drives, gas engine drives, and induction motor drives towards high-efficiency electric drives that have low energy costs and are environmentally friendly--and this trend is becoming increasingly apparent. In response to this demand and in order to enable the widespread usage of its servo packages in general industrial machinery, in 2010 AIDA began selling servo system packages consisting of servo motors and peripheral equipment based on its independently developed servo motor technologies.
While leveraging our field of expertise--designing optimal production systems to meet differing requirements--we foresee the use of our servo press packages not only for presses but also in a wide variety of fields, including general industrial machinery (injection molding machines, extrusion machines, die casting machines), construction equipment, food processing machinery, vehicles, ships, windpower generators, and hydroelectric generators. Moreover, it may not be long before our servo packages are also incorporated into environmental and green energy fields that have even higher energy conservation and efficiency requirements.
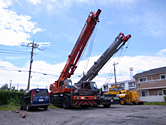
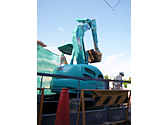
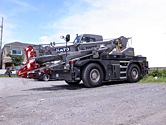
Total Solutions for Forming Systems
Majority of our products are custom-built machines. In order to provide customized solutions to help clients manufacture products of a higher quality at a lower cost, our research and development team harmonizes our expertise in manufacturing, controls and tooling technologies. We are also continuously improving our problem-solving abilities to cover the entire range of production systems through the in-house development and manufacture of various automation devices and industrial robots. Thus, as a forming systems builder, AIDA strives to provide optimal solutions demanded by its customers using its vast knowledge of the entire production process.